MRP definition
- The MRP is a stock planning and management system, based on computer support that answers the following questions: What, how much and when should it be manufactured (Unicen, 2003).
- It is a computer procedure to convert the master program for the production of final products into a more detailed program of raw material and components used in these products. The program indicates quantities of each item, when to replenish and when to deliver to ensure compliance with the master production program (Groover M., 1997, p. 993).
- There are 4 necessary data entries that an MRP system requires for proper operation, and are as follows:
-
Master Production Program (MPS).
-
Materials List (BOM).
-
Explosion of materials (MRP).
-
Inventory status (Domínguez G. et al., 2016, pp. 114).
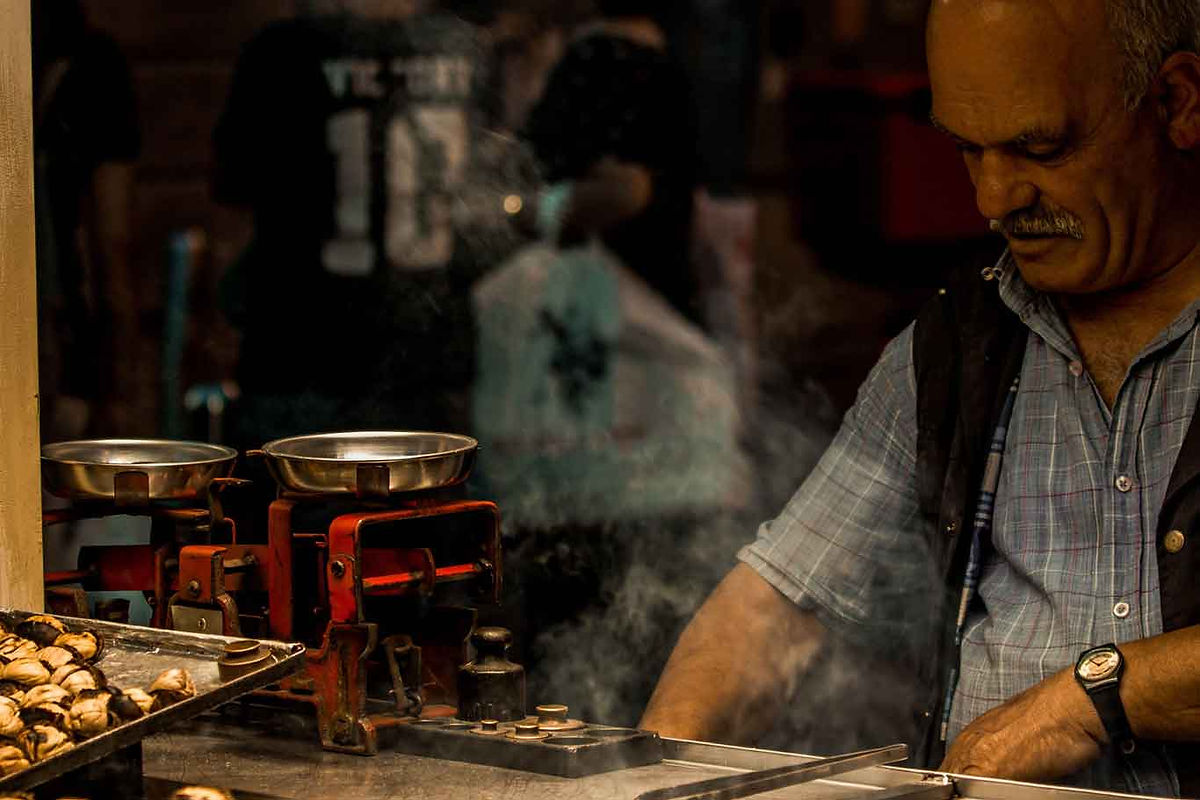
-
Systemic integration of areas:
-
Costs, MPS, BOM, MRP and inventories.
-
Accounting administration based on production cost system.
-
Database management on products, customers, suppliers and payroll of workers.
-
Management of variable costs and indirect manufacturing costs.
-
Personnel assistance management.
-
Determine the payment role of workers.
-
Determine overtime and supplementary hours.
-
Fault management and justification of staff.
-
Management of staff vacations.
-
Determine BOM at all levels based on a modified N matrix.
-
Determine stock of products and components.
-
Security stock management for products and components.
-
Determine scenarios about user hypotheses.
-
Determine material needs.
-
Determine MRP of products and components up to 4 levels.
-
Determine ABC inventory analysis.
-
Operating profit management.
-
Open source (unrestricted edition, except for commercial use).
-
Determine 3 types of work termination:
-
Eviction, untimely dismissal and resignation,
-
Under regulations of Ecuadorian Law.
-
Determine total unit cost.
-
Total unit cost management by time horizons assigned by the user.
-
Proforma management.
-
Issuance of invoices (PDF backups, automatic sending by e-mail via Outlook and management of invoices for data storage.
-
Management of production orders, inventories and production forecasts by 2 methods:
-
Exponential smoothing and linear regression.
-
Determine CMT analysis under the MRP philosophy.
-
Additional general accounting management (account catalog, daily book, majorization of T accounts, checking balance and general balance).
-
Multiuser
-
Error handlers
-
User guides (video tutorials).