¿Qué es un sistema MRP?
- Sistema MRP
- 10 dic 2019
- 9 Min. de lectura
Actualizado: 13 dic 2019
#sistemamrp #recursosmateriales #controldeinventarios #mrpenexcel #sistemadecontroldeinventarios #sistemadecontroldeinventariosenexcel #sistemadeinventarioenexcel #sistemadeinventariodeproduccion #inventariodeproductosexcel #controldeproduccion #controldeproduccionxls #sistemamrpenexcel
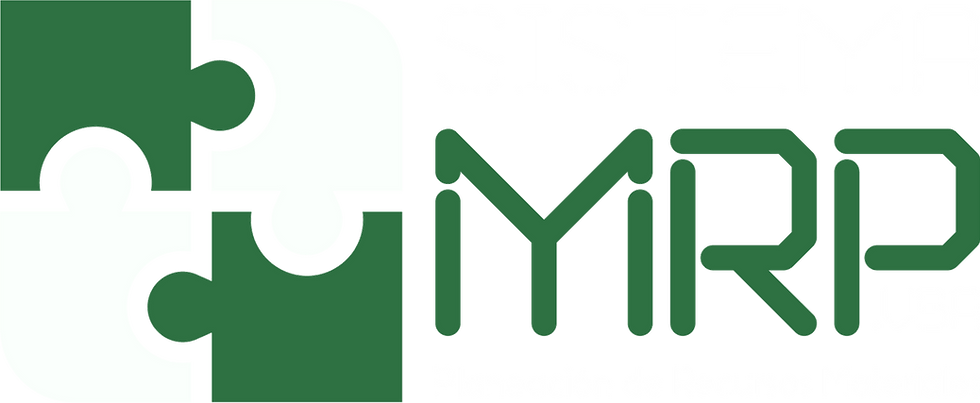
Hola emprendedores y entusiastas productivos. En este artículo vamos a conceptualizar el acrónimo MRP (Planificación de recursos materiales) y vamos a observar mediante teoría cuáles son los pilares fundamentales para el correcto funcionamiento de este sistema, para su óptima aplicación en la gestión y control de inventarios. Esto nos servirá para definir los datos principales con los que un sistema MRP puede alimentarse y funcionar de forma acertada.
Bien, entonces comencemos por la teoría.
MRP
Según Iñiguez (2003), la planeación de requerimientos materiales (MRP) es un programa computacional cuyo objetivo es determinar cantidades de materias primas, componentes, subensambles y ensambles requeridos para los horizontes de planeación productiva. El procedimiento de MRP está basado en dos ideas fundamentales:
- El MRP crea órdenes de producción con demanda dependiente.
- Las necesidades de cada artículo a través de demanda independiente y la estructura del producto (plazos de elaboración y fabricación).
Según Unicen (2003), entonces el MRP es un sistema de planificación y gestión de stocks, basado en un soporte informático que responde a las siguientes preguntas: Qué, cuánto y cuándo se debe fabricar.
Siguiendo a Groover (1997), MRP es un procedimiento de computación para convertir el programa maestro de producción de productos finales, en un programa más detallado de materia prima y componentes utilizados en dichos productos. El programa indica cantidades de cada artículo, cuándo reabastecerse y cuándo entregar para garantizar con el cumplimiento del programa maestro de producción.
Ahora, a juzgar por Muñoz (2009), MRP es el resultado es un programa que se utiliza para que los insumos, partes y componentes estén disponibles cuando el proceso de producción los demande, evitando almacenamiento innecesario.
Conforme con Gitman (2003), en otras palabras, MRP es una técnica de administración de inventarios que relaciona conceptos de tamaño de lote económico y una computadora para comparar necesidades de producción de acuerdo al inventario disponible.
De acuerdo con Domínguez et al. (2016), existen 4 entradas necesarias de datos que requiere un sistema MRP para su correcto funcionamiento, y son las siguientes:
- Programa maestro de producción (MPS).
- Lista de Materiales (BOM).
- Explosión de materiales.
- Estado de inventarios.
Programa maestro de producción (MPS).
Según Groover M. (1997), el programa maestro de producción (MPS) es un programa que enlista los productos a fabricarse, cuándo deben terminarse y en qué cantidad. La cantidad enlistada de productos, se debe por 3 requerimientos:
- Pedidos de clientes. Ventas a un cliente.
- Demanda prevista. Demanda pronosticada en un periodo de tiempo.
- Partes de repuesto. Categoría que puede ser excluida por no tratarse de productos completos.
De los requerimientos antes expuestos, la categoría de la demanda prevista, es la que genera mayor interés, pues es la que con frecuencia dominará el programa de producción.
Demanda prevista y pronósticos
Según Masini & Vázquez (2014), la demanda que se prevé para un periodo de tiempo, está relacionada con los pronósticos. Un pronóstico debe tener datos de calidad, es decir, deben tener las siguientes características:
· Confiables y precisos. De fuentes confiables.
· Pertinentes. Representativos.
· Consistentes. Mantener patrones históricos.
· Periódicos. Datos deben ser recolectados con periodicidad.
Los pronósticos se dan a partir de datos históricos, y, a partir de ello, se realiza el siguiente procedimiento:
1. Recopilación de datos. Los datos deben ser adecuados, y constituye el paso más difícil.
2. Reducción de datos. Datos pertinentes.
3. Construcción del modelo. Ajustar los datos a un modelo de pronóstico adecuado; lo cual se realiza mediante la mezcla óptima entre los siguientes factores: tipo de patrón encontrado en los datos, marco de tiempo (inmediato, corto plazo, mediano plazo, largo plazo), disponibilidad de los datos, precisión deseada y facilidad de operación.
4. Extrapolación del modelo. Ejecución del pronóstico y obtención de errores de pronóstico, resultado de la comparación de valores pronóstico y valores reales obtenidos.
Los métodos de pronóstico, se clasifican en cualitativos y cuantitativos. Los métodos cualitativos son utilizados generalmente cuando el marco de tiempo es de mediano a largo plazo mientras que los métodos cuantitativos son utilizados para marcos de tiempo más estrechos. Por tales efectos, se tomarán en cuenta únicamente modelos cuantitativos, los cuales se dividen de la siguiente forma:
· Análisis de series de tiempo: métodos de promedio móvil, métodos de suavización, descomposición de series de tiempo, metodología Box – Jenkins.
· Modelos causales: modelos de regresión, modelos econométricos.
De los muchos modelos de pronósticos, en este artículo vamos a mencionar dos de ellos, uno cuando no hay tendencia aparente de los datos: método de suavización y otro cuando los datos muestran una tendencia: modelo de regresión.
Método de suavización
Según Montemayor (2013), los métodos de suavización, se clasifican de acuerdo al patrón de la serie, y pueden ser de patrón horizontal, de tendencia o estacional.
Método de suavización exponencial simple
De acuerdo con Keat & Young (2004), este método es apropiado cuando no hay tendencia aparente en los datos. Si existe alguna tendencia pronunciada, este método generará pronósticos pobres.
Conforme con Aguirre (1994), este método aplica una constante, asumiendo poca tendencia de la serie de datos; la constante definida como α (entre 0 y 1) determina el peso dado a los valores de la serie. Entre más pequeño, más peso tendrán todos los valores. La mayor dificultad de este método es encontrar una constante α más adecuada, por ello hay paquetes de software que incorporan un procedimiento auto correctivo denominado de Chow para la búsqueda automática de valores óptimos de la constante de suavizamiento.
Según Marqués (2010), como regla práctica, si los datos presentan fuertes fluctuaciones, se deben utilizar valores pequeños de α; si se llegasen a utilizar valores altos de α (mayores a 0.5), es muy posible que los datos puedan presentar tendencias, por lo que utilizar este método ya no sería adecuado.
Modelo de regresión
Según Montemayor (2013), estos modelos buscan predecir variables dependientes a través de variables controlables o independientes. Para efectos de simplicidad, se tomará en cuenta el modelo de regresión lineal simple, el cual toma en cuenta una variable independiente.
Regresión lineal simple
De acuerdo a Hamdy (2004), este análisis que determina la relación entre una variable dependiente (demanda de un producto A) y una independiente (tiempo). Para que exista un buen ajuste lineal entre variables, su coeficiente de correlación debe ser mayor o igual a 0.75.
Siguiendo a Vélez (2003), este es un modelo que, para utilizarlo con validez estadística, es necesario contar con alrededor de 25 datos históricos.
Lista de materiales (BOM).
Según Gitman (2003), la lista de materiales (BOM) es un listado de partes y materiales que se necesitan para la elaboración del producto terminado.
De acuerdo con Krajewski & Ritzman (2000), es un registro donde figuran todos los componentes pertenecientes a un artículo, sus relaciones padre – componente y las cantidades de uso correspondientes al diseño y proceso.
Explosión de materiales.
Según Chapman (2006), la explosión de materiales es el proceso de calcular para cada período la demanda dependiente, en función de la demanda independiente, basándose en la lista de materiales. La serie de cálculos que se plantea en este apartado son los siguientes:
- Necesidades brutas. Representan las necesidades del componente en los respectivos períodos de tiempo. Es el resultado de multiplicar la demanda prevista y los requerimientos de la matriz N.
- Pedidos pendientes o recepciones programadas. Pedidos ya hechos de componentes, y que se encuentran pendientes de recibirse. Parámetro susceptible a modificaciones y que puede ser automatizado, con una previa revisión de la persona que manipule.
- Necesidades netas. A partir de las necesidades brutas, se descuenta existencias disponibles y pedidos pendientes de recibirse.
- Lanzamiento de pedidos planificados. Según Anaya (2007), esto representa la cantidad que se va a producir en un periodo para que después de transcurrido, esté listo para su recepción.
Estado de inventarios.
Según Miranda et al. (2012), el estado de inventarios es un listado de todos los artículos de demanda independiente y dependiente. Es un estado que se actualiza en función de pedidos emitidos y recepciones planificadas. Indica la cantidad de cada material que se va a pedir en cada periodo de tiempo, y constituye base directa para el informe final de un MRP.
Es un estado que muestra los artículos de demanda independiente y dependiente, en cuanto a su disponibilidad actual o stock, stock de seguridad (si existe) y el tiempo de suministro o fabricación para cada artículo y sus componentes individuales.
Stock
Según Escudero (2010), el stock son inventarios físicos que tiene la empresa hasta su utilización o venta. Pueden ser de dos tipos: Industrial (materia prima, productos en proceso y productos terminados) y Comercial (mercancías).
La gestión de stock industrial es de especial importancia para el trabajo de investigación, y sucede en tres niveles:
- Stock de materia prima. Productos adquiridos para entrar en el proceso productivo.
- Stock de productos en proceso o semielaborados. Se encuentran al final de un proceso y a la espera del siguiente. Esto se debe a la mala organización del proceso y producción en grandes lotes.
- Stock de productos terminados. De acuerdo con Cuatrecasas (2011), este último nivel es aquel que ha pasado por todas las etapas del proceso productivo y se encuentra a la espera para su venta.
Stock de seguridad
Según Rey (2013), el stock de seguridad es aquel aprovisionamiento de inventario que se añade para evitar un agotamiento de stocks como consecuencia de retraso en las entregas de pedidos o aumento imprevisto de las ventas.
Siguiendo a Cuatrecasas (2005), el stock de seguridad también es denominado como stock de reserva, stock de protección, stock de acopio. La cantidad de stock de seguridad puede depender de la variabilidad de la demanda, del plazo de entrega y del riesgo que se está a dispuesto a estimar. Existen ciertas situaciones en las que se necesita establecer el stock de seguridad, como son:
- Demanda aleatoria y plazo de entrega conocido.
- Demanda conocida y plazo de entrega aleatorio.
- Demanda y plazo de entrega aleatorios.
- Si el sistema de aprovisionamiento se realiza mediante fechas preestablecidas.
Bien, de la teoría podemos extraer la siguiente metodología para desarrollar un básico, aunque buen, sistema MRP.
Metodología para desarrollar un sistema MRP
Se requiere una serie de datos para poder implementar, integrar y ejecutar un sistema MRP. Entre los más importantes, son los siguientes:
- Base de Datos. Serie de datos primarios que se requieren para la alimentación y retroalimentación del sistema MRP (clientes, proveedores, productos y lo referente a costos de producción).
- MPS (a través de demanda pronosticadas y/o las órdenes reales de producción de clientes).
- BOM (a través de lista de materiales).
- Explosión de materiales (a través de necesidades materiales o recepciones programadas, necesidades brutas, pedidos pendientes, necesidades netas y lanzamiento de pedidos planificados o MRP).
- Estado de Inventarios (a través de stock, stock de seguridad, CMT y Análisis ABC).
- Software utilizado. Programa que se utilizará para la aplicación del sistema MRP. En este caso, Excel integrado con VBA y XML.
Los inputs o datos de entrada que puede tener un sistema de planificación de recursos materiales (MRP) básico son las siguientes, y se exponen en la figura a continuación basado en el gráfico de Domínguez et al. (2016).

Con esta estructura principal, podemos realizar un esquema general más detallado de datos
que alimentan a unos u otros elementos, como por ejemplo se muestra en la figura que sigue; por supuesto, esto solo es algo general, el mismo puede profundizar en elementos, según los datos que necesite controlar la organización; sin embargo, para proyectos o emprendimientos que inician actividades es más que suficiente.

Si deseas observar el funcionamiento y ventajas de un sistema de gestión y control de inventarios MRP desarrollado con Excel, VBA y XML bajo la teoría y el esquema observado con anterioridad puedes visualizar el siguiente video:
Bien, eso ha sido todo por el día de hoy. Por mi parte, me despido, sin antes desearles un genial día. Y, no se olviden de sonreír, para recordar que la vida sonríe siempre.
Referencias bibliográficas:
Aguirre A. (1994). Introducción al tratamiento de series temporales. Aplicación de las ciencias de la salud. Ediciones Diaz de Santos S.A. Madrid, España.
Anaya J.J. (2007). Logística Integral: la gestión operativa de la empresa. Editoriales ESIC. Tercera edición. Madrid, España.
Chapman S. (2006). Planificación y control de la producción. Editorial Pearson Prentice Hall. Primera edición. Universidad autónoma de México. Naucalpan de Suárez, México.
Cuatrecasas LL. (2011). Organización de la producción y dirección de operaciones. Sistemas actuales de gestión eficiente y competitiva. Editorial Diaz de Santos S.A. Madrid, España.
Domínguez G., Domínguez A. R. & Torres J.A. (2016). Didáctica y aplicación de la Administración de operaciones. Contaduría y Administración. Instituto Mexicano de Contadores Públicos. México.
Escudero J. (2010). Operaciones administrativas de compra venta. Administración y gestión. Editorial Paraninfo S.A. Madrid, España.
Gitman L. (2003). Principios de administración financiera. Editoriales Pearson. Décima edición. Naucalpan de Juárez, México.
Groover M. (1997). Fundamentos de manufactura moderna. Materiales, procesos y sistemas. Editorial PRENTICE-HALL. Primera edición. Naucalpan de Juárez, México.
Hamdy A. (2004). Investigación de operaciones. Editorial Pearson. Séptima edición. University of Arkansas, Fayetteville. Traducido en México.
Iñiguez Aguilar, F. J. 2003. Desarrollo de una planta de salsa y aplicación de herramientas de ingeniería para su mejor desempeño. Tesis Licenciatura. Ingeniería Industrial. Departamento de Ingeniería Industrial y Textil, Escuela de Ingeniería, Universidad de las Américas Puebla. México.
Keat P.& Young P. (2004). Economía de empresa. Editorial Pearson Prentice Hall. Cuarta edición. Insituto Tecnológico y de Estudios Superiores de Monterrrey. Monterrey, México.
Krajewski L.& Ritzman L. (2000). Administración de operaciones: estrategia y análisis. Editorial Pearson. Quinta edición. Naucalpan de Juárez, México.
Marqués F. (2010). Modelos financieros a través de Excel. Editorial RC libros. Madrid, España.
Masini J. & Vázquez F. (2014). Compendio de Modelos cuantitativos de pronósticos: el primer paso de las decisiones tácticas, es predecir la demanda. Innovación, ingeniería, valor. Advanced value group. México.
Miranda F.J., Rubio S., Chamorro A. & Bañegil T. (2012). Manual de dirección de operaciones. Editorial Paraninfo. Primera edición. Madrid, España.
Montemayor G. (2013). Métodos de pronósticos para negocios. Editorial digital Tecnológico de Monterrey. Instituto Tecnológico y de Estudios Superiores de Monterrey. México.
Muñoz D. (2009). Administración de operaciones. Enfoque de administración de procesos de negocios. Editorial Cengage Learning. Santa Fe, México.
Rey J. (2013). Proceso integral de la actividad comercial. Administración y finanzas. Segunda Edición. Editorial Paraninfo S.A. Madrid, España.
Unicen (2003). Sistema de información para administración de operaciones. [En línea]. Recuperado de la página: http://www.exa.unicen.edu.ar/catedras/modemp/12_MRP.pdf
Vélez I. (2003). Decisiones empresariales, bajo riesgo de incertidumbre. Editorial Politécnico Gran colombiano. Grupo editorial Norma. Bogotá, Colombia.
Comments